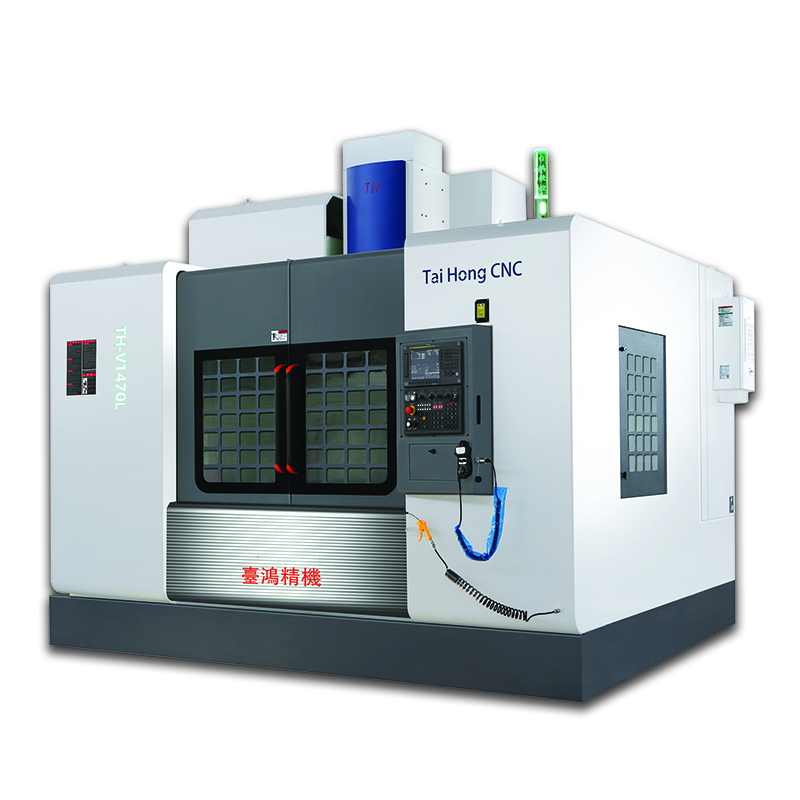
实践证明,当切削速度提高10倍,进给速度提高20倍,远远超越传统的切削“禁区”后,切削机理发生了根本的变化。其结果是:单位功率的金属切除率提高了30%~40%,切削力降低了30%,刀具的切削寿命提高了70%,大幅度降低了留在工件上的切削热,切削振动几乎消失;切削加工发生了本质性的飞跃。根据目前机床的情况来看,要充分发挥先进刀具的高速加工能力,需采用高速加工,增大单位时间材料被切除的体积(材料切除率Q)。
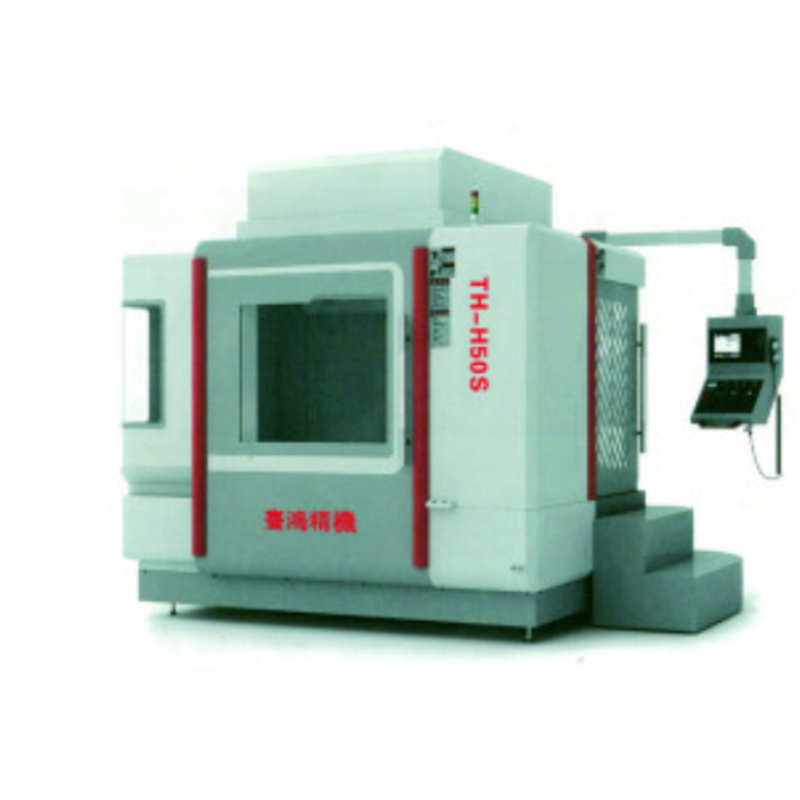
与此同时,出现了各种新型可转位刀片结构,如用于车削的高效刮光刀片、形状复杂的带前角铣刀刀片、球头立铣刀刀片、防甩飞的高速铣刀刀片等。可转位刀片进入了材料、涂层、槽型综合开发的新阶段,可根据加工材料和加工工序合理组合材料、涂层、槽型的功能,开发出具有佳加工效果的刀片,以满足高速、高寿命切削加工生产技术的不同要求。
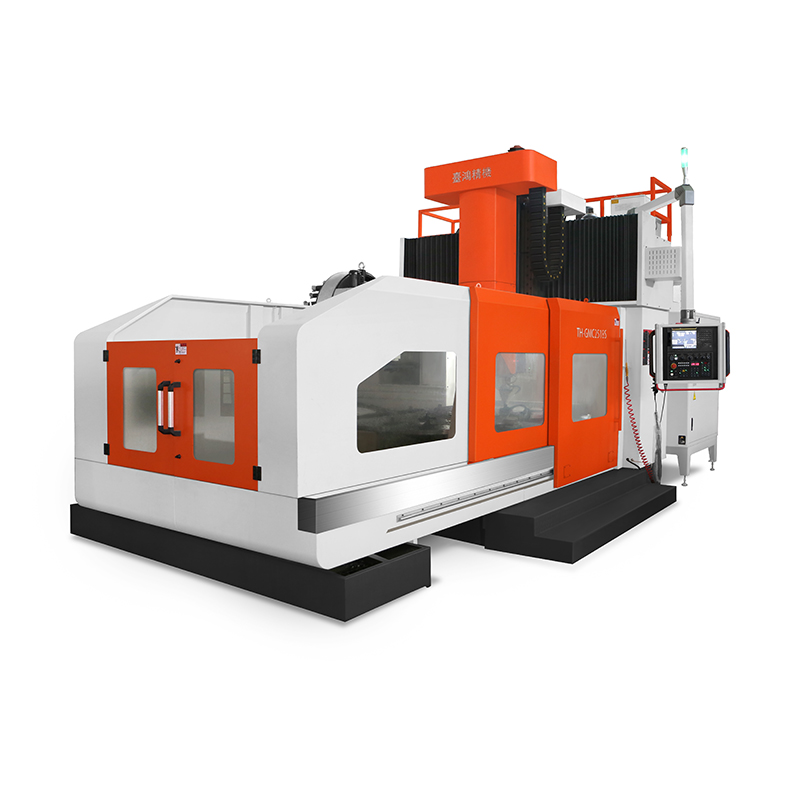
刀片精度低,跳动量太大,面铣刀加工的平面光洁度将降低,甚至出现沟状。高精度数控机床上刀片的跳动量应控制在2~5μm。随着数控机床的发展,相应出现刀片的表面改性涂层处理(基体为高速钢、WCo类硬质合金、Ti基类金属陶瓷),很大程度上提高了刀片精度。
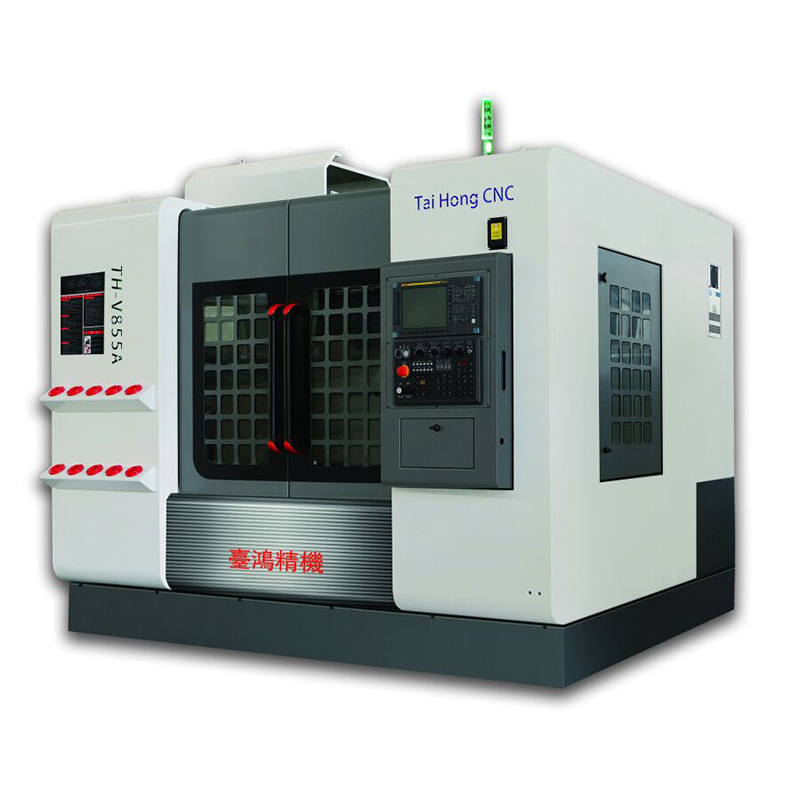
在数控机床切削加工中,金属切削刀具的作用不亚于瓦特发明的蒸气机。制造刀具的材料必须具有很高的高温硬度和耐磨性,必要的抗弯强度、冲击韧性和化学惰性,良好的工艺性(切削加工、锻造和热处理等),并不易变形。